Work Order Management – Are your Suppliers delivering consistently?
Work Order Management – Are your Suppliers delivering consistently?
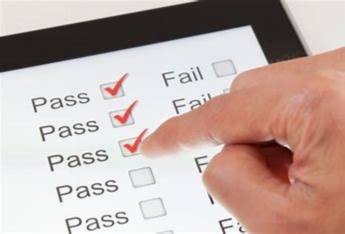
Breakdowns will happen, what matters is how you respond to fix them
With any large network of sites, especially where your key assets come into contact with the end-users and the weather, you will need to deal with the inevitable need to arrange for repairs.
This can be manageable when your equipment portfolio is new, shiny or under warranty, especially if you have just a few sites. However, as your sites age, and as your estate grows in size, the sheer volume of repairs and interventions you need to make quickly becomes immense. After a while you don’t even notice how long you are having to work each day just to try to keep up with the status of each repair.
The result is often that despite your hard work and effort, having visibility of your workforce or contractors is difficult. It’s hard to prioritise and get all the tasks done promptly, and as a result your assets or sites are often left unavailable, leading to customer dis-satisfaction.
On top of these issues, the world is now a much faster moving place in terms of technology and sustainability. When you need to make strategic decisions about which equipment to replace, upgrade or write-off (due to sales, cost or carbon footprint) you do not want to be stuck having to chase every work order with the same level of effort, just to keep the lights on.
Being Smart
There are various computer-aided facilities management (CAFM) systems or maintenance management systems (MMS) available which can offer significant benefits. Designed and used appropriately, they can revolutionise the way in which a Facilities Management team, and a business as a whole, functions.
Achieving improvement in results usually requires doing things differently, and not just “the way we’ve always done it”. But to secure the buy-in and support your business will need to overcome their fear of change, they need to clearly understand and define the reasons for making an improvement to the way things function.
We have overseen the design & implementation of smart work order management systems at businesses of all sizes, including multinational corporations. Here we explain the best ways to approach the introduction of smart work order management systems, including how to prepare others in the organisation for the prospect of change.
Managing the Change
If an organisation makes the decision to do something about its work order management, then this is often for one of two general reasons.
The ideal type are those businesses who have a clear idea of what they want to get from the organisational changes associated with a new approach (and smart technology or system to provide the vehicle for this). This is usually based on proactive thinking and analysis of business data, which has revealed gaps or inefficiencies within existing processes. They will have a clear idea of what they want to do differently. They understand their processes, they know what information is missing and they often approach the project armed with data-driven insights and sound analysis of contextual facts. They will normally clearly define the areas where change is required and will understand what these changes need to achieve, from the top down. They will aggregate, share and use this information to drive innovation. However, it is important to realize that these types tend to be the exception and not the norm.
More often, there is the second type of business. They want to change because they see there are developments in the sector. They recognise that their existing solutions are not fit for purpose and have a fear of being ‘left behind’. Alternatively, they might have never had the experience or awareness of what is possible to achieve or may simply be so overwhelmed with the volume of work that they have not had the time to investigate options. This more reactive type of business are less well prepared. They often have unrealistic expectations of what a CAFM software system can achieve for them, in terms of the time and effort that is required to land them properly. A CAFM is, after all, just a system. It requires humans to understand how to set it up to work for your organisation, how to apply it, and how to use it effectively. This type of business puts their faith in the misconception that implementing CAFM will streamline operations overnight and prompt immediate cost savings. In effect, they think they can spend a few moments implementing the system, “out of the box”, and then the job will be done. But this approach does not consider the bigger picture.
By clearly setting out reasons for change, the implementation of new smart workflows will go a lot more smoothly, and provide the organisation with key measurable targets, critical for validating decisions and demonstrating a return.
What can go wrong?
An upside-down (or back to front) approach to implementation causes the biggest issues.
Beginning the implementation process and then later working out what is required from your new system or software package will not deliver the results you need.
In this instance you may suddenly find everyone in the room has become an expert on CAFM system implementation, despite never having experienced it. Listen to those who know how it works from experience and your journey will be a lot smoother.
Setting the Foundations
Do not underestimate the importance of planning before you begin. There is a lot you can do from the outset to get the most out of your transition to improved work order management, and so that key stakeholders fully support it.
Define your stakeholder group and begin to map out the reasons for change and the expected benefits that each might achieve.
Define goals and see how they impact on existing processes. Gather data and insights from across the business to inform a gap analysis.
And be realistic about what can be achieved, as well as the time and resources that will be required to get there.
All these steps will help limit change requests once development has begun.
A clear approach to work order management
We tend to find that a root cause of the challenges most businesses face is not having a clearly thought through and implemented workflow that is robust, understood by everyone and efficient.
There are various factors which inform the workflow mapping, which we can broadly describe as being people, system or process related.
By taking the time to understand the current workflow, and in the process understanding what does or does not work well, and the different teams’ perceptions and understanding of this, you can all start to really build a cohesive picture of the root causes of some of your current challenges and garner buy-in and build motivation to realise a smarter way of working.
Our advice is to ensure that your organisation sees the process as a worthwhile investment.
Spend time with experts who have been through it all before to really help you examine the way you work. If something is broken it can be difficult to determine exactly what it is or to find solutions when you are immersed within it, day to day. Learn from the insights and lessons of others and ask for help.
People, systems, process
Whether or not you ultimately choose to implement some form of technology / software like a CAFM or MMS system, to track and administer your workflow, the interaction of people, processes and system is best documented. If part or all of the process can be automated in some way then the benefits are only amplified, and the resource required to keep on top of things is much more manageable.
Spending time remapping the works management processes has been proven to provide a really solid foundation for transition: enabling and empowering individuals, teams, partners and suppliers to understand the impact and potential of implementation.
A single source of truth
Once the workflow is clearly understood then the process of optimising a system to work for your business can be successful. Being able to track all activity in one place provides not only resource and efficiency benefits, but also the certainty and consistency that having one source of trustworthy information delivers.
Taking control & Informing decisions
Once your optimised workflows are in place you will start to see benefits very quickly. Initially this will include the benefits of certainty and transparency, and over time, you will reap the benefits of trend management and resource efficiency.
Your teams will also enjoy the opportunities a clear work order management provides, allowing much more emphasis on the sorts of strategic and value adding work which can re-focus your business towards:
- longer term planning,
- more predictive maintenance,
- tasks which result in reduced downtime,
- focussing on projects to deliver energy savings, or
- managing asset upgrades.
Leading the Transition
Working with an experienced consultant who has experience of working for a relevant operating organisation can be invaluable to provide direction to steer your various stakeholders through the transition and to overcome fear of and resistance to change. A governance board created specifically for the implementation project can be extremely useful. It can steer the project toward tangible objectives, challenge assumptions and unite behind a valued and common goal.
A governance board or group of key stakeholders can also be very important in making sure the core system workflows and processes remain consistent across multi geography businesses where there is nearly always a cultural preference to do this “locally”.
Making changes to your workflow without the right and clear objectives leads to implementation without evaluation, or without a sound understanding of why you needed to manage your workflow in the first place. Unless everyone recognises and aligns behind the core problems you are trying to solve, it can be a recipe for disaster. A firm handle on collating and using the right types of data is invaluable and integral to the process.
Benefitting from your newly managed workflow
A well thought through and carefully managed work-flow transition project will have profound benefits for you. These will be felt by your people, by how much smoother and clear your processes are, and in the confidence you have in the information available from your systems.
Ultimately you and your team will be able to challenge and interrogate data, and then use it to unlock learnings and validate assumptions. You’ll find it easier to justify expenditure, to map and measure improvements.
All of this will have a significant impact on the decisions you are able to make and your ability to keep your network functional, and ready for use by your satisfied customers and end-users.