Demonstrate compliance and task validation
Establishing a “source of truth” to demonstrate compliance and task validation
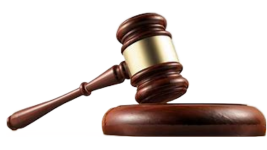
How do you know your network is fully compliant?
Every operator wants to be assured that their network is up to date, and that all of their equipment has been fully maintained and complies with all legal requirements and internal group policies. As estates grow in size, the volume of equipment and associated tasks required to monitor, test, inspect or examine each asset at the optimum frequencies creates a significant potential for data overload and arduous administration.
In a previous article we discussed the benefits of workflow management systems to track reactive breakdowns. Many of the same considerations and benefits also exist for defining, planning, scheduling and tracking planned tasks which are required either as preventative measures or to prevent breakdown. In some cases they may also be a legal requirement.
What do I need to do?
A maintenance regime is made up of the following key components.
- You must comply with legal requirements to do specific tasks
- You should create a balanced preventative maintenance plan which includes pre-meditated tasks to intervene before failure
- When equipment fails, you need to have the ability to quickly diagnose and fix it, preferably at the first attempt
- If you are able to track all of the above and link this to specific equipment in the form of an asset record, you can strategically plan for asset replacement and upgrade. (See our earlier article)
- Make sure you are not just tracking the cost and uptime of your equipment but also the revenue it is generating for your business
Clearly a single source of truth to track all of the above is beneficial, and we have discussed this in a precious article.
Why maintain proactively?
Maintaining your equipment before it fails has a number of key advantages:
- Predicting downtime will lead to better availability for your customers
- Properly planned equipment interventions are much more cost effective
- You can plan for when to undertake intervention to avoid disruptions at at peak trading periods
- Having a better understanding of how your network performs gives you better cost certainty for today and the future
Proactive maintenance is primarily based on two components – tasks which must be done to ensure legal compliance (often labelled as compliance tasks) and PPM tasks which are designed to ensure the equipment runs to its optimum levels.
Compliance Tasks
Some requirements are set down in regulations, and are very clearly defined in accordance with industry standards. These are often at set frequencies, with a clear expectation of what records should be kept. For example, the requirements for periodic Electrical Installation Condition Report (EICR) are well defined. (There are many other examples of tasks which have a defined requirement, frequency and output expectation.)
Other compliance tasks however may be based on risk assessment or interpretation of the regulations. Whilst these may not be conducted at intervals which are clearly defined in the regulations, the regulations often use language such as “should be maintained in accordance with manufacturer’s recommendations” or “a risk assessment must be completed at an appropriate frequency”. There is therefore a requirement for the operator to make a policy based decision to determine what tasks they will undertake to comply with these requirements, and how often they will carry them out.
Planned & Preventative Maintenance (PPM)
Careful PPM planning, using clear and well analysed equipment data can deliver the advantages mentioned earlier. PPM normally includes a balance of recommended tasks, for example where suggested by the manufacturer or by industry guidance, coupled with information from breakdowns, linked to the equipment asset, which can be used to identify whether more or less intervention is required to prevent costly failures from occurring. As we mentioned before, understanding the relationship between your assets and your revenue means you may choose to increase the amount and type of PPM works for higher performing or critical equipment, with the costs balanced out by prolonging the PPM intervals on assets that are not delivering the same high performance revenues.
Why do tasks need to be validated
Whether for compliance or PPM tasks there is benefit to knowing that the task has been completed properly. To do so typically requires a number of key steps:
- The operator should have a clear policy identifying what tasks are required, how often they shall take place, to what standards and for which specific assets.
- A suitably competent person must be engaged, either internally or via a specialist trade contractor. Importantly, a thorough procurement and vetting process must verify their credentials.
- You then need to ensure that tasks are appropriately scheduled, booked in with site, and completed on time, and that they have spent sufficient time to complete the tasks properly.
- Once the initial task is completed, a report should be issued promptly, identifying the results of the task and, importantly any remedial actions required. (The equipment has not been verified as compliant until all remedial actions are completed, and we will look at this aspect in more detail in another article.
- Ideally, when records are received, you will have a way of tracking and verifying that procedures have been followed, and that the tasks have been carried out in accordance with the specification.
- Furthermore, have they provided the right records? Has someone competent validated them and do they include for all of the equipment on your site?
Common Pitfalls
We’ve come across many discrepancies when it comes to poorly validated works. This is often found when a new client asks us in to review the state of their compliance. Examples can include:
- The contractor has set their own specification for the works they will undertake, and the client / operator has not had the expertise and/or resource to check and confirm that the method of completing the task is appropriate to the need.
- The individual performing the task does not have the appropriate qualifications or competence.
- The record or certification of the task are either poorly documented, recorded on the wrong type of document, missing key assets or, in some cases can be missing completely.
- A report is filed, and the job closed out as complete, even though the report found a number of actions to be completed. These unfortunately might never be followed up.
What can go wrong if a task is non-compliant?
Statistics often demonstrate that when issues or accidents occur, a number of minor failings have often accumulated over time.
Should such failings lead to a serious incident, then, without proper records, the operator would have a significant challenge defending any action taken against them. Where there are records that show that actions have not appropriately been taken or verified, that can also lead to problems, whereby a typical statement might be something along the lines of “the company was warned about ‘risk’, but failed to act accordingly”. This is often a more serious offence, especially if the lack of validation conflicts with your own written internal policies.
It goes without saying that any failure is punishable by the courts, and also, if it involves a breach in health and safety, then the relevant authority or HSE is also likely to take action.
The solution
Evenlode Roadside has many years of experience of procuring, tracking and validating compliance and PPM tasks.
A system that provides a “single source of truth” can be invaluable in managing these issues, but the solution involves much more than just about choosing a software package. The wider tasks required include:
- development of clear policies & procedures,
- procuring and the performance management of competent providers,
- using appropriately trained and competent personnel,
- designing and implementing clear administrative workflows.
We would be delighted to discuss your specific needs. Please contact us for more information.