Manage remedial actions through to completion
Manage remedial actions through to completion
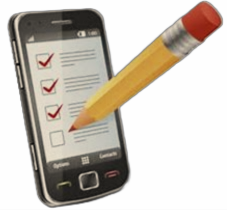
In a previous article we looked at the importance of completing and validating compliance tasks, and, for ensuring that PPM activities have been completed and validated correctly. One of the common failings that is often cited in any public hearings following an unfortunate incident is along the lines of the statement
“the company was warned about ‘risk’, but failed to act accordingly”.
Failure to manage remedial actions can occur when
- A formal risk assessment has identified outstanding works or management actions, which subsequently become overdue
- A scheduled service report identified faults or further works, which ought to be performed to maintain the equipment’s condition, but they’re never completed
- An internal H&S audit identifies failings or areas for improvement
- An enforcement or prohibition notice is issued by a regulating body
- Following an equipment breakdown, the asset is bring back into service but other parts are required to complete the task fully
So what can go wrong?
Whereas systems are available that can schedule the initial planned task, the ability and diligence to track any follow up actions through to completion is often a real headache for operators.
It is very common to find that if a deep dive audit is undertaken, and unless a professional approach is in place, many outstanding remedial actions can go unresolved for some time, and in some cases might never be tidied up. The issue is a lot more common than senior management might normally expect it to be.
Clearly, if a remedial action plan has identified a significant issue, then for legal compliance it needs to be addressed.
Unfortunately for operators who have many sites, and especially those whose network is growing fast, the growth often comes before adequate means of control are implemented. The risks for these organisations is significant and it only increases as the estate grows.
What makes following up remedial actions so difficult?
The challenges can exist in many parts of the workflow process, including:
- Specialist contractors may not be contracted to complete the repair
- There can often be no actual way of identifying and logging that further actions are required
- The review of initial task reports is often not automated. In these instances, the requirement for a remedial action can be simply overlooked and not followed up.
- Maintenance teams are over-stretched with little time to check the reports.
- Where validation has been outsourced, the outsourced provider’s staff are not adequately competent, resourced not incentivised / motivated to identify actions.
- Once the initial task is “completed” the status report or dashboard shows a completed task, so the impetus to follow through is often lost in the quagmire of the ever growing lists of jobs.
- Assuming the task is logged for follow up, the system for tracking and verifying is not sufficiently robust.
- Often remedial actions require works to be quoted for, and it is common that robust administrative processes both for soliciting and validating quotes is sorely lacking.
- Managerial actions are often not followed up if they are owned by personnel in other departments.
- There is no clearly defined system which accurately tracks the tasks and reports them in one single source of truth.
How do you know when the remedial task is done?
As we have indicated, there are multiple reasons that tasks might not be getting done. But how do we know the tasks are being completed?
One way is to select and implement an intelligent software system, that is carefully designed and implemented, with appropriate governance embedded within the operator’s organisation. Importantly, the supply chain also need to be brought along over time, and specialist input is normally required to ensure this is done and their behaviours reinforced.
Some, but not all systems can now clearly show the actual status of a task, in granular detail, and in real-time. This can distinguish between a task that has been scheduled, initially completed and those tasks where remedial actions are now outstanding. Clever reporting mechanisms can keep track of who is responsible for completion of the task, and issue reminders and managerial reports to keep key people aware of the status.
The use of geo fencing in todays software means tasks can only be validated or closed out when the operative is still on site as opposed to competing a retrospective closure of tasks at the end of the working day.
Is it compliant or not?
We have previously indicated that until all the remedial actions are completed, the equipment is most likely not compliant.
All operators will want to know that their estate is safe for its customers, so having a firm handle on this is becoming more important.
A solution
Evenlode Roadside has experience of working with many multi-site operators and understands the pros and cons of many different software systems to ensure that equipment is compliant. Solutions to managing remedial action compliance in a holistic manner can include a thorough end to end audit and deep dive into existing records, policies and processes to understand the true status of your compliance. A solution that compliments or enhances your internal processes and governance can then be established.
The end to end compliance process includes having:
- Clear policies and procedures
- Competent advice over technical matters, from industry experts
- Equipment risk assessments
- Control measures that include appropriately scheduled and specified tasks
- Responsible parties who are either internal or who are professionally procured accredited specialists
- Defined resources and regular training
- Thorough records of all tasks, inspections, servicing, tests and examinations
- Prioritisation of resource to complete the most pressing tasks
- Evidence of regular auditing of remedial task completion
- Proactive monitoring and follow-through to prevent actions being completed late
A key benefit of a thorough thus type of approach is the real-time visibility that you can achieve. You can gain the confidence that the data you are being shown is true, accurate and up to date. Not only can you gain compliance, you can also keep ongoing control of it. Often these benefits can be realised by your in-house teams if they are provided with the right level of experienced support and guidance. This is a particular benefit where your teams are stretched.
The way you approach the management of your compliance ought to be independent of your suppliers and contractors. This ensures that you have control and there are no conflicting interests in the timely reporting of information.
Ultimately, applying the solutions mentioned above reduces the operators costs, administrative burden and corporate risks.
Please contact Evenlode Roadside for more information to significantly improve the compliance of your network.